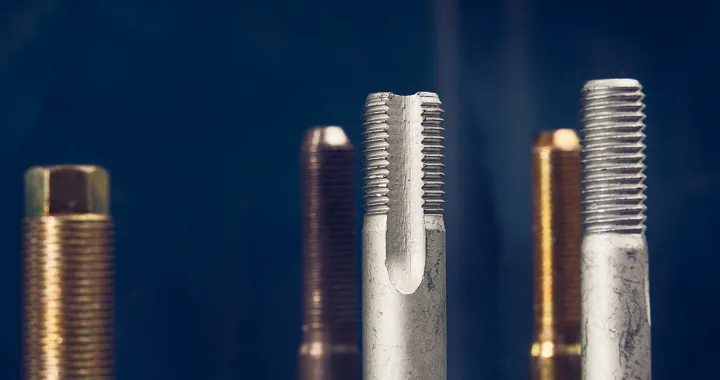
Tomorrow’s fastening solutions
What products will be requested in ten years? What do our customers need tomorrow to bring their products to market and how can we improve on what our customers use today?
Designing for today, tomorrow, and the future
Technological breakthroughs are transforming the way we live and work. The demands of a rapidly advancing society push industries to innovate at lightning speed, from electric vehicles to smart cities, to sustainable manufacturing. At Bulten, we help companies reach their goals and innovate faster.
With a multi-layered approach we ensure that we’re always delivering what our customers need, when they need it —today and tomorrow. Our Innovation teams focus on the solutions we anticipate our customers will need in the next decade and our Application & Product teams create tomorrow's products, working closely with clients to design fasteners that fit the products they’re developing right now. Additionally, our factory Engineers take customer blueprints and transform them into high-quality, efficient products ready for production today. This way we ensure we’re always ahead, delivering what our customers need—when they need it.
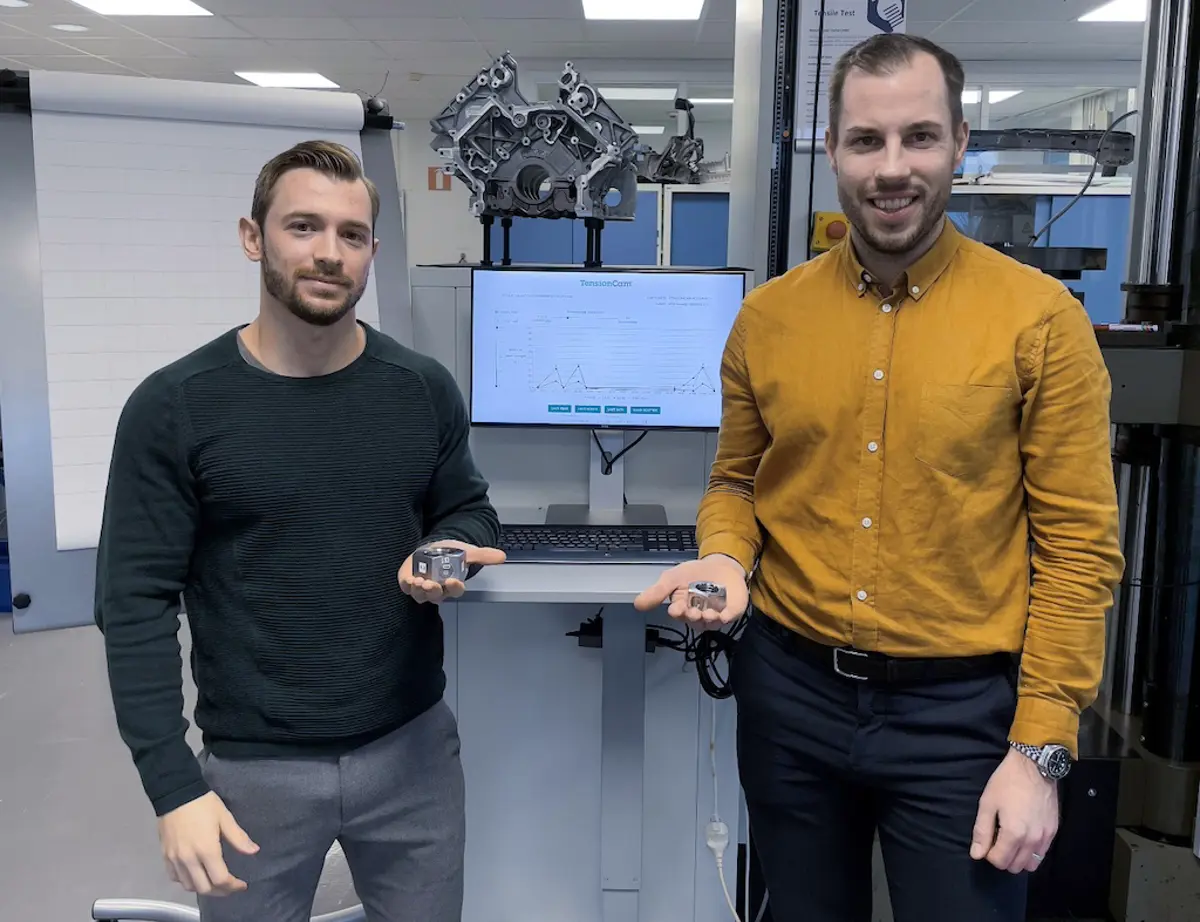
Our teams of forward-thinkers
Bulten drives innovation through several teams that collaborate to create progress across our timelines. We have two centers that are focal points for this; Advanced Technology Center (BATC) in Sweden and the Innovation Center (BIC) in Poland.
Here, experts in materials, testing, application and design, create cutting-edge fastener solutions that undergo rigorous testing before entering production.
These teams also enhance our processes and provide advanced support to ensure superior product performance. The work is executed with three dimensions in mind; Speed, Sustainability and Functionality.
Sustainability, Functionality, and Speed
Together, our teams are driving transformation forward, responding to the urgent need for faster time to market, environmentally responsible solutions, and future-proof technology. We call this the Innovation Box and we aim to ensure all our solutions fall within it.
Our ambition is always to create lighter, smarter fasteners that work better, while also minimizing resources and carbon emissions.
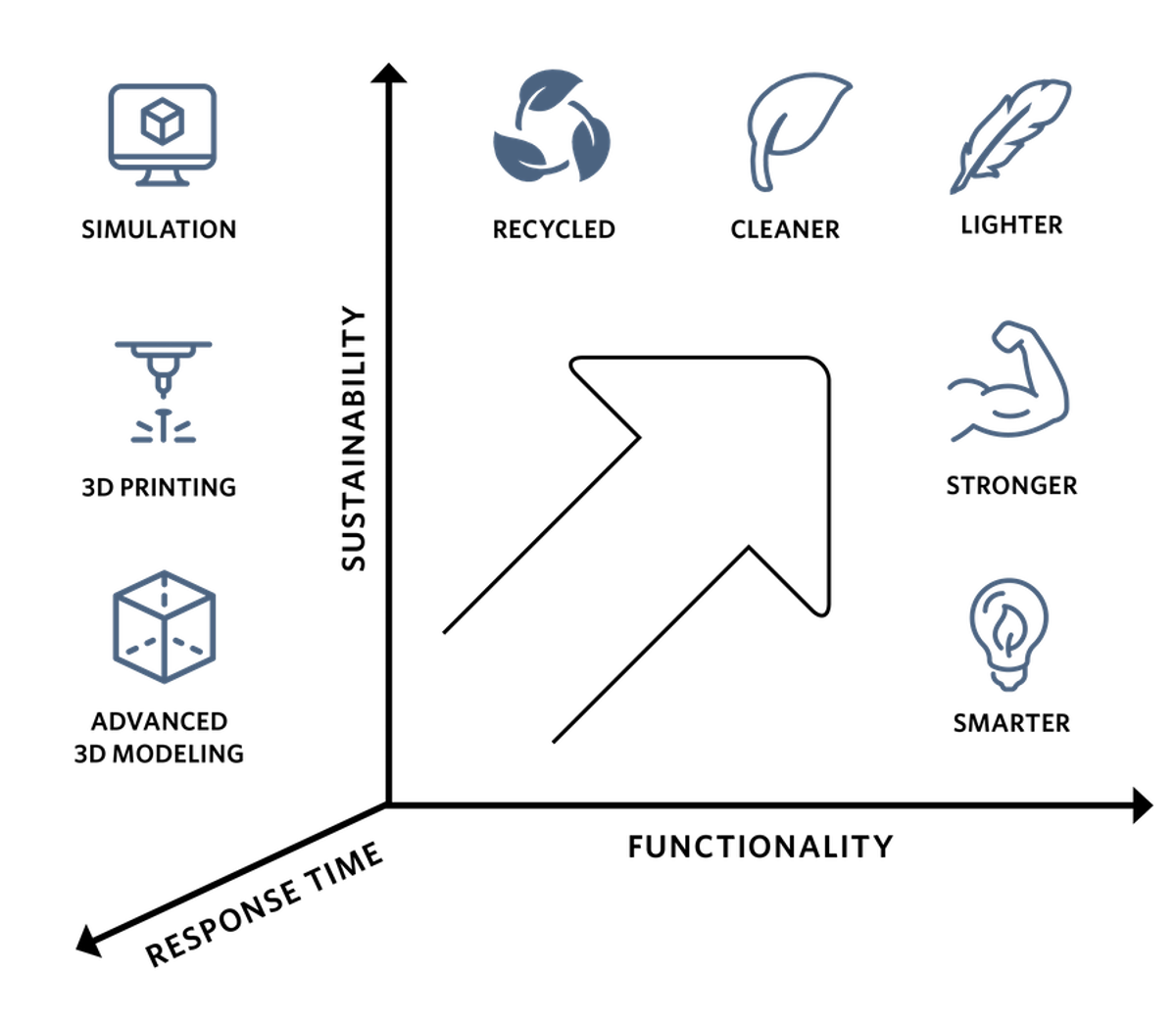
Meeting tomorrow at speed with fast prototyping
Our 3D printing and rapid prototyping capabilities allow us to quickly transform ideas into prototypes. This means we can help our customers get to market faster, meeting the increasing demands of a world that won’t wait. Whether you’re developing new electric vehicle components or improving infrastructure, our fast prototyping and agile production help you stay ahead.
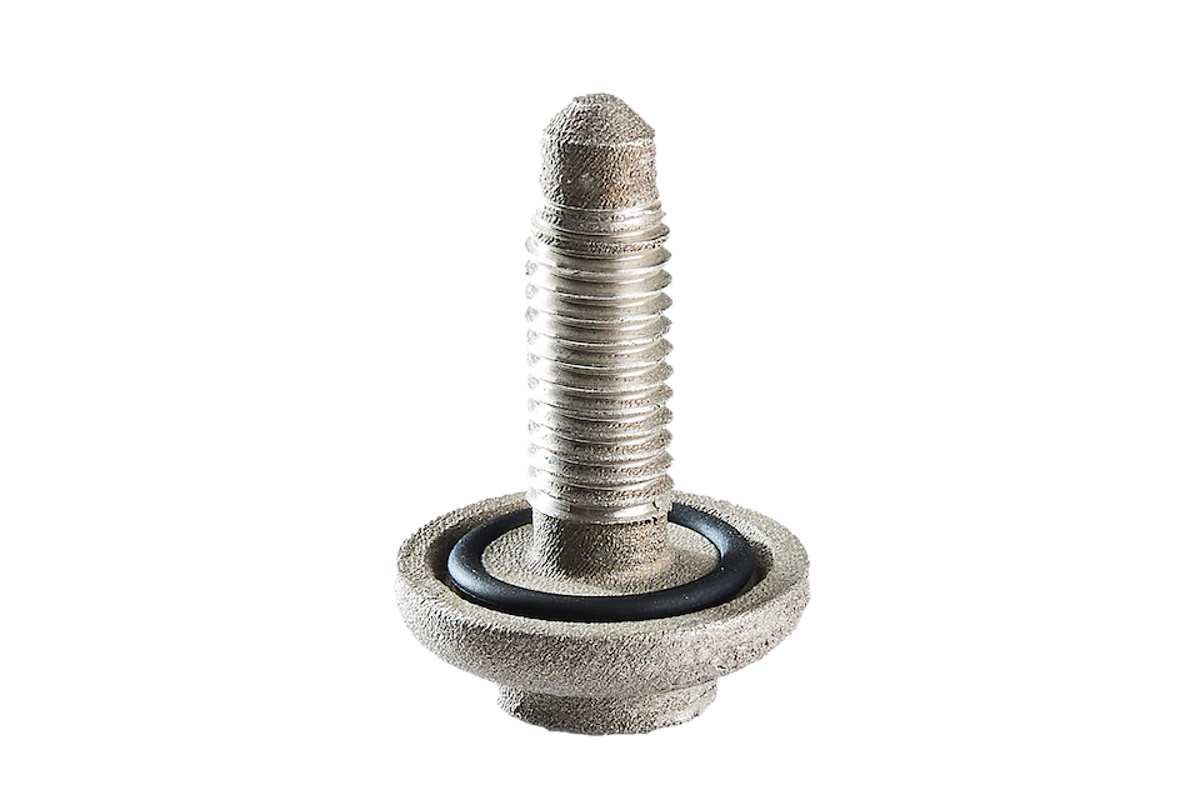
Examples of rapid prototypes
Small batch of hybrid metal-plastic components
Our ability to combine technologies is exemplified in this project, where we produced a batch of 10 hybrid components consisting of metal and plastic.
The metal part was machined, while the plastic was 3D printed. Notably, the metal surface was coated—a rare achievement for such small sample volumes. This case demonstrates our rapid prototyping capability, blending materials seamlessly to deliver functional prototypes at exceptional speed.
Flexible polymer components for Automotive customer
In collaboration with a university, we delivered 400 split grommets 3D-printed with flexible polymer material. This is a perfect example of how we can scale 3D printing for relatively high volumes in the prototyping phase, providing a viable alternative to traditional processes when volumes are too small for standard manufacturing. The flexibility in both materials and process allows us to respond quickly to specialized needs.
3D metal printing with surface calibration
We delivered 10 metal screws to one customer through 3D printing, completing the process with surface finishing and thread calibration. The result was precise, functional prototypes ready for immediate testing, produced in a short timeframe. By integrating post-processing, we provided high-quality, production-ready parts with rapid turnaround.
Creating a greener future with sustainable fasteners
Every product we develop is engineered with environmental impact in mind. From utilizing scrap-based steel to drastically reducing energy consumption through cold forging technology, we’re committed to greener manufacturing without compromising performance. Our mission is clear: to create the future’s most advanced fasteners in the most responsible way possible.
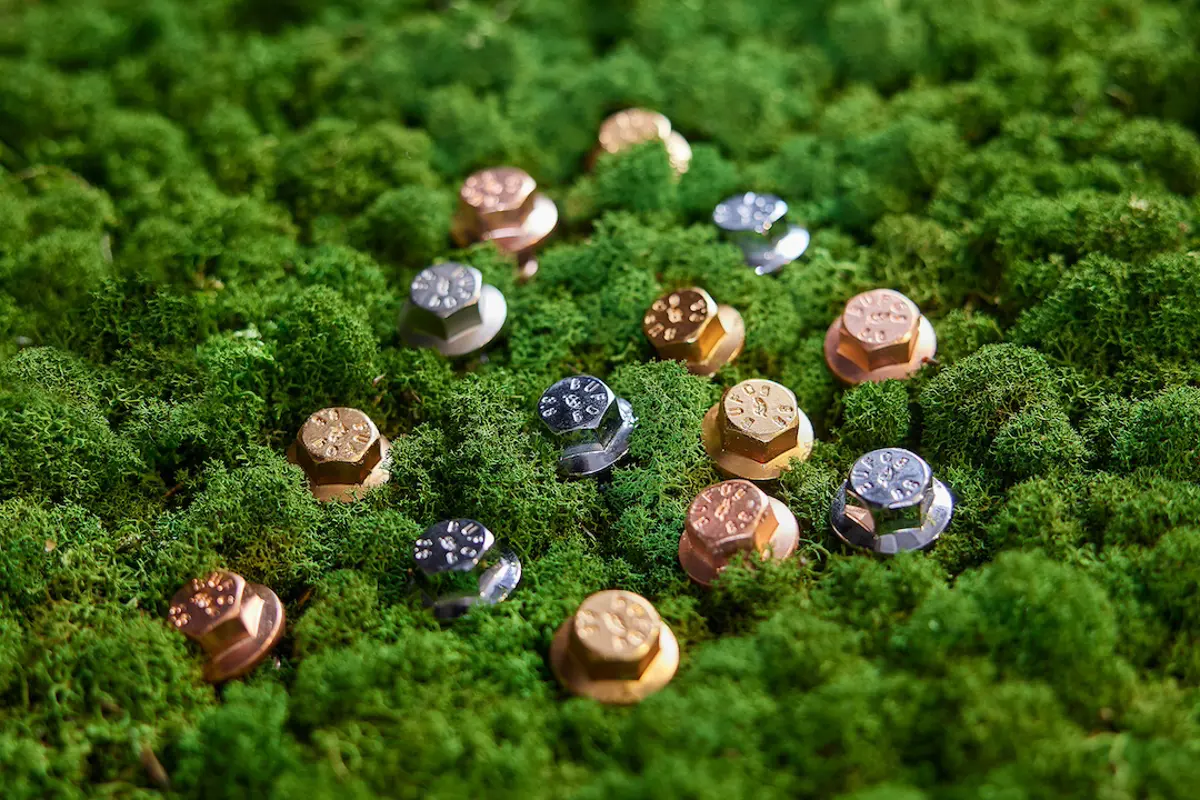
BUFOg – Yesterday’s materials are tomorrow’s solutions
By incorporating 60–80% recycled scrap from end-of-life products and using fossil-free electricity, we strive to reduce the output of carbon dioxide to 300 kg per ton in the steels we use for our products. This is truly a milestone on the way to carbon neutrality.
BUFOe – The next generation of sustainable fasteners
Our BUFOe product family has a distinct sustainability profile, reducing energy consumption and lowering emissions during production. BUFOe products utilize a combination of material and forging process that eliminate the need for heat treatment, resulting in a 50% energy save and 30% lower carbon footprint. For our customers, this translates to true environmental efficiency.
Shaping the future with smarter fasteners
We’re continuously developing smarter and more functional fastening solutions that meet modern needs. Innovations like RFID-enabled fasteners ensure installation accuracy, while new design features like integrated sealing functions support electric vehicle advancements. These solutions are created not only for today but with future connectivity and sustainability in mind, recognizing that even small components can drive significant progress.
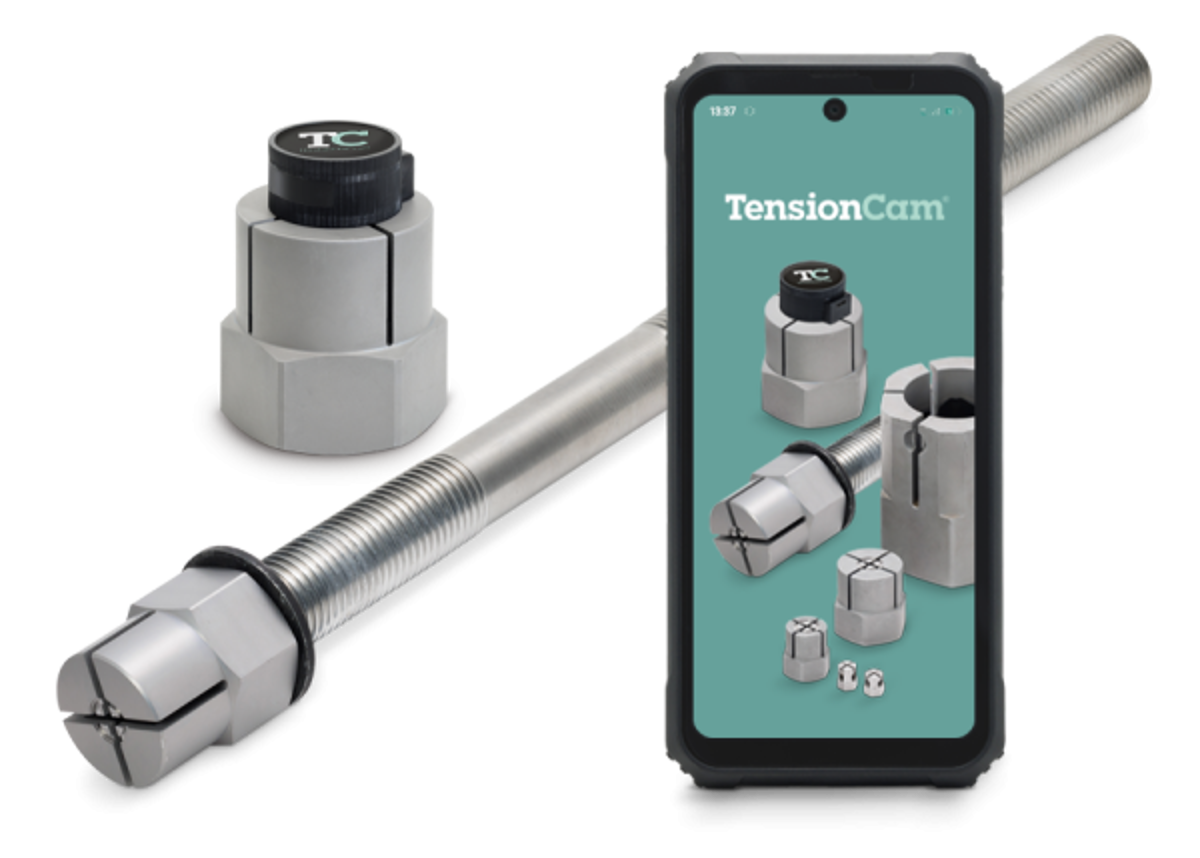
TensionCam – A part of Bulten
TensionCam offers advanced sensor technology that monitors clamp loads in critical screw joints, providing real-time data for better maintenance planning. Used in industries like wind power, railways, and water treatment, it enables businesses to detect issues early, reducing maintenance costs and preventing delays or accidents. With its data-driven approach, TensionCam transforms traditional maintenance practices, making them more proactive and efficient.
Read more about TensionCam